You are here: > Eng.Support > Equipments > Vacuum Generating Device > Liquid Ring Vacuum Pump
Liquid Ring Vacuum Pump
Similar to other pumps, a Liquid Ring Vacuum Pump (LRVP) has a bladed impeller attached to a center hub.
Typical centrifugal pumps increase the operating pressure of pumped fluid: the fluid at the pump suction port (flange) has a low pressure value, whereas after passing through the various pumps impellers stages, the fluid is discharged from the pump's discharge port (flange) with a higher pressure. Unlike centrifugal pumps, LRVPs are used to pull air out of low pressure vessels so that the vessel pressure drops below atmospheric pressure value and vacuum conditions are created.
The major construction difference between liquid ring vacuum pumps and other pumps is that this impeller is off-set from the center of the pump. Consequently, the blades on the top of the pump are closer to the outside wall than those located at the side of the pump and those located at the bottom of the pump. The compression is performed by the liquid ring as a result of this relative eccentricity.
The eccentricity leads to partial filling and then partial emptying of each rotor chamber during a revolution. This partial filling and emptying action leads to a piston action within each set of rotor or impeller blades. Pump parts are assembled in such a way so as to allow gas in when the rotor chamber is emptying of liquid and discharge gas once the compression has been completed.
Liquid ring vacuum pumps typically use a liquid seal to achieve a vacuum. The most widely used liquid is water – typically used once through and rejected to drain. Quite often, a cooling water system is also in place so as to dissipate the heat produced during operation. At this case, a portion of the liquid in the casing is continuously discharged with the gas, collected in a separator vessel and led to a heat exchanger. The cooled liquid is then introduced back to the pump casing in order to remove the heat of compression.
More information on the design of liquid ring vacuum pumps (LRVPs), is presented in the latest version of Heat Exchange Institute (HEI) standards for Liquid Ring Vacuum Pumps.
Figure 1 - Schematic of a liquid ring vacuum pump
One of the terms used when designing a liquid ring vacuum pump (LRVP) system is pull-down time, i.e. the time needed to achieve the desirable operating vacuum from atmospheric pressure.
Applications of Liquid Ring Vacuum Pumps
LVRPs are widely used in power plants, petrochemical, pharmaceutical, food manufacturing and health sectors. Typical process applications for vacuum pumps include use in main steam condenser evacuation systems, distillation columns, evaporative coolers, chemical reactors, laboratory analysis etc.
Advantages of liquid ring vacuum pumps
-
Easy maintenance
-
One moving part, no metal-to-metal contact in the compression chamber, no internal lubrication required
Disadvantages of liquid ring vacuum pumps
-
Environmental concerns with disposal of condensed liquid waste
-
High power consumption, compared to other vacuum devices, for example steam ejectors.
-
Pumps are usually oversized so as to cope with high liquid seal temperature, thus further increasing energy consumption. It is quite common that An increase of liquid seal temperature by just a few degrees Celsius can reduce LRVP capacity by as much as 20-25% and thus reduce the maximum vacuum achievable.
How to improve the performance of a LRVP system
Performance of a liquid ring vacuum pump can be improved by following the below mentioned recommendations:
-
Installation of solenoid valves on seal and cooling water supply and interlock these valves with the pump motor. This will prevent water wastage when the pump motor is not working.
-
Installation of a sealing liquid heat exchanger if the seal liquid temperature is high. This of course will drive costs higher but will lead to efficiency improvements.
-
Examine the possibility of using alternative liquid seals (other than water) that can eliminate waste water production and further improve vacuum performance.
-
Installation of Variable Speed Drives (VSDs) on pump motors so as to reduce electricity costs as well as minimise pump wear and tear.
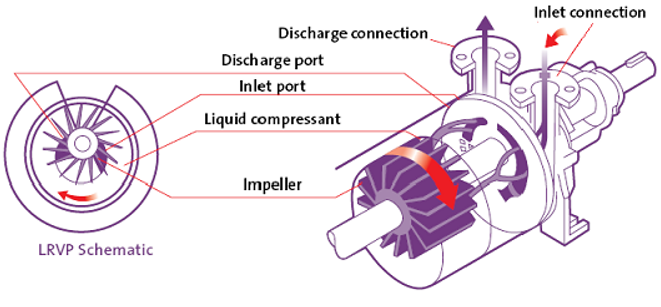